徐有芳 刘华 王艳东
(济南钢铁集团总公司,山东济南 250101)
摘 要:济钢炼钢厂在炼钢主体设备上采用多点干油泵系统,并同步优化油品,改善了设备的润滑状况,提高了设备的使用寿命,实现了炼钢设备管理的良性循环。
关键词:润滑;炼钢设备;多点干油泵;润滑油脂
润滑是保证炼钢设备正常运行的必要条件。炼钢机械多处于高温、重载、多汽和多灰尘的工作环境中,因而对润滑要求苛刻。传统的润滑系统设计大多采用干油集中润滑泵站,通过给油器分配到各润滑点的供油方式。而国产泵站、给油器及压力操纵阀常因使用不当或质量不过关,造成润滑系统瘫痪,引起设备润滑不良、故障增多,影响生产。
1 济钢主体生产设备润滑状况分析
济南钢铁集团总公司(简称济钢)炼钢设备的润滑状况大致可分为四种:
(1)国产主体设备引进国外润滑系统。如1996以产的4#板坯铸机,其润滑系统装置采用日本进口的干油集中润滑系统采用自动供油控制、单线片式给油器的供油方式,对该系统须加强维护,保持它的先进性,并作为每次检修的重点来对待,保证从振动系统到Z后一组辊道都得到良好的润滑,以实现主机设备较高的作业率。
(2)国产设备采用国产润滑系统。如1990年投产的3#板坯铸机,其润滑系统采用的是传统的干油集中润滑泵站,通过给油器逐级分配到各润滑点,由于分配器不过关,一处不通、全线瘫痪。其油质是二硫化钼钙基脂,泵送性能较差,因此刚刚投产时,虽然都调拭好,但使用不到一年时间就无法运行,其润滑可靠性也不理想,维护比较麻烦。
(3)只有主机设备而没有考虑设备润滑系统。如70年代初的两台小板铸机、1998年投产的方坯铸机,各润滑部位只是装配时一次性手工涂抹,致使设备运行过程中的故障不断、作业率很低。
(4)有些设备润滑方式陈旧,产生其它的副效应。如25t转炉耳轴轴承,设计时采用传动的稀油润滑方式,由于密封问题很难解决,供油压力大、漏油量大;供油压力小也有漏油现象,常因钢渣喷溅而引发火灾事故。经过解体轴承座发现,轴承内部润滑不到位,对轴承寿命产生不利影响。
综上所述,除4#铸机润滑设备比较先进且效果较好外,其余设备润滑大多采用手工一次性涂抹润滑脂,润滑设备几乎为零,润滑油品也多采用传统的油基脂,粘附性差、易乳化、易流失,闪点、熔点低。因润滑设备简陋不能为生产设备连续性供油,且检修时一次性涂抹润滑脂,不能使油品建立起压力以形成一定厚度的油膜,因而常出现因润滑不及时、不到位造成故障停机。备品备件寿命短、检修难度大、成本费用高的现象普遍存在。
2 方案设计及实施
1996年6月,根据济钢炼钢厂设备运行状态,首先确定以方坯铸机拉矫机为突破口,在滚动轴承副上采用电动干油泵系统,即适用性强的DDB型多点干油泵,且同步优化油品。
采用多点干油泵的主要依据是:
(1)多点干油泵出油口通过管路直接与润滑点连接,这样不需分配器,管路控制也不需要电磁换向阀、压力操纵阀。因而避免了以上元件发生故障造成润滑系统失效的可能。
(2)多点干油泵安装位置可靠近润滑点,润滑管路短,压力损失小。多点干油泵工作压力为10MPa,能Z大限度地提高泵的工作效率。
(3)多点干油泵易于现场维护管理。当某一点出现故障时,不影响其整个系统工作,设备电器配置简单、故障少。
(4)采用多点干油泵投资少,在具有相同润滑点的系统中,其费用仅为干油集中润滑系统的1/3。
方坯铸机为四机四流,每一流拉矫机有10个润滑点,在每一流拉矫机上选用一台DDB-10型多点干油泵。通过无缝钢管和高压胶管使泵与润滑点相连接。根据现场实际情况,对多点干油泵的出油口接头进行了改造,泵的工作压力为10MPa,连续向拉矫机辊轴承座提供具有压力的润滑脂,改善了轴承运动副的工作条件,大大提高了拉矫机使用寿命,原每流每月更换2~3台拉矫机减少到改造后每80~90天更换一台,同时也降低了检修劳动强度和维修成本,经济效益十分可观。
方坯拉矫机采用多点干油泵润滑效果突出,为此又先后在方坯振动系统(72点)、大包回转台(12点)安装了两台DDB-18型干油泵。在3#板坯铸机,扇形段轴承润滑(92点),拉矫机(72点),振动系统(18点)和大包回转台(24点),以及两台R6-1000板坯连铸机拉矫机(28点)也安装了干油泵。这样,5台连铸机上共安装16台多点干油泵,随后又在三座600t混铁炉传动系统各安装两台DDB-10型多点干油泵,成功地解决了混铁炉润滑不良的问题。
多点干油泵的控制可由专人定时通过手动或自动来实现启闭油泵;自动控制方式为定时启闭油泵或使油泵间隙运转。
多点干油泵在济钢炼钢厂良好的运行,为济钢第三炼铁厂混铁炉和济钢炼钢厂3#铸机二切割辊道采用该润滑方式提供了实用经验。
3 扩大干油润滑成果,改革润滑方式
济钢三座25t转炉耳轴两侧轴承内径为750mm,外径为1090mm,工作转速为1rpm,由于工作性质决定了转炉在小于360°的范围内往复运转。原润滑方式为稀油站润滑,通过对轴承解体检查发现,轴承滚柱与内外圈运动副之间稀油并没有形成真正的油膜,加之耳轴托圈密封很难保证,进入轴承的稀油泄漏现象时有发生,在运动副之间产生锈斑,轴承滚柱磨损不均,造成轴承柱碎裂,致使如此关键设备的轴承达不到正常使用寿命就被迫更换,造成人力、物力和财力的极大浪费。为此,在考虑到转炉转动速度、负载等因素和托圈耳轴具有通水冷却的情况下,提出转炉耳轴轴承由稀油润滑改为干油润滑,这也为全国同类型转炉耳轴轴承使用干油润滑开创了先例。通过一年多的运行,效果良好,杜绝了因钢渣液喷溅引发外漏稀油着火事故的隐患。
转炉耳轴轴承干油润滑采用DB-63型单线干油泵,通过自制分配器,均匀有效的向轴承6个方向润滑,润滑到位、油膜保持良好。
此外,在4#铸机大型蒸汽抽引风机上也采用了DB-63型单线干油泵来润滑风机转子轴承。考虑到天车滚筒及吊勾组加油困难,采用了DB-63型单线干油泵,也都取得了良好的效果。
4 适应炼钢设备要求,改进润滑脂
传统的钠、锂基润滑油脂,存在着粘附力差、不能抗强淋水冲击,易流失,易乳化的缺点;高温辐射下低闪点,理化性能严重破坏,在冶金设备润滑的应用范围逐渐萎缩。取而代之的高闪点、粘附力强的润滑油脂相继出现,脲基脂就是其中的一种,该脂的理化指标、泵送性能适合济钢炼钢厂设备润滑要求。在选用多点干油泵的同时,济钢选用了新港1#脲基脂,从而优化了润滑油品。该脂在3#铸机拉矫辊轴承上应用,多点干油泵工作15min,送油300g。在密封不良情况下,可连续工作128h;在密封良好条件下,连续工作可达670h,均未出现异常现象。在工作中,由于密封不严,既使有杂质进入轴承座内,油脂由米黄色变为灰褐色,轴承滚道内仍有油膜存在,轴承游隙基本未变。实践证明,脲基脂在高温下,具有较高滴点、闪点,在强淋水冲击下,具有极好的抗水和防锈润滑性能。新港1#脲基脂与1#极压锂基脂理化性能比较见表1。
表1 新港#脲基脂与1#极压锂基脂理化性能对比
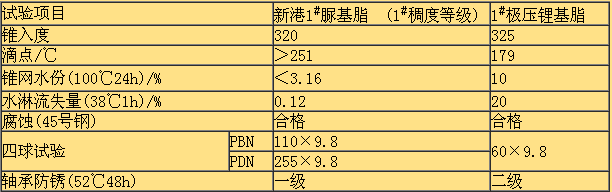
在完善设备润滑设计改造的同时,济钢炼钢厂加大建章立制的工作力度,制订了《润滑油(脂)管理制度》、《多点干油泵操作及加油制度》、《液压系统巡回点检制度》,使润油管理有章可循,规范操作行为,真正做到“依法管理”。这不仅提高了设备润滑的科技含量,也优化了冶金设备的基础管理。
参考文献:[1]机械设计手册。机械工业出版社,1992.1
来源:《山东冶金》2000年第6期